February 1953 QST
Table
of Contents
Wax nostalgic about and learn from the history of early electronics. See articles
from
QST, published December 1915 - present (visit ARRL
for info). All copyrights hereby acknowledged.
|
Magnetic ceramics have been with us
for a long time - probably forever as far as most people that use them these days
are concerned. When this article was published in a 1953 issue of QST magazine,
ferrites for use at RF frequencies were a new, breakthrough phenomenon. Take a look
at inductors used in vintage radio equipment and you will find either air or solid
iron as the permeable filler elements in most instances. Whereas iron might have
a permeability of 100-150, the new magnetic ceramics exhibited permeabilities up
to 4,000 at 1 MHz, and even higher for lower frequencies. Modern alloys and
compounds provide permeabilities of more than 50,000 for special applications. Such
high values allow physical size and weight of inductors and transformers to be greatly
reduced. Also, since high permeability does a better job of constraining magnetic
fields within their geometries, less shielding is required to prevent crosstalk. A
plethora of resources are available on the Internet for design guidelines.
Magnetic Ceramics: Ferrites
The Latest in Magnetic Materials for R.F.
By F. E. Vinal, W1GXJ
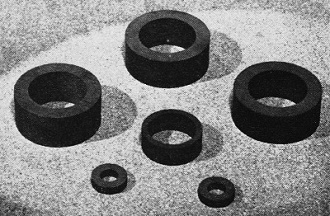
Typical ferrite cores for toroidal inductors.
(Photo courtesy Sprague Products Co.)
Through current advertising items and several articles which have appeared recently,
some in electronics journals, it is becoming increasingly evident that an entirely
new series of electronic components exists based on the magnetic ceramics or ferrites.
These materials, many of whose trade names have been obtained by taking various
liberties with the Latin word for iron - ferrum - have opened new horizons for the
professional design engineer, but they are no less a challenge to amateur ingenuity
and the home experimenter.
It is the purpose of this article to introduce magnetic ceramics to the rank
and file of the amateur fraternity; from there, one hesitates to predict what may
result. No attempt will be made to be fundamental about the source of the magnetic
effects. The writer, who is a chemist gone astray, does not follow all of the abstractions
which are available on the internal workings of atoms, but friends who are theoretical
physicists tell me that quantum mechanics are required to give an adequate explanation
of the origin of the magnetic effects in ferrites; further, there are adequate theoretical
publications now available dealing with these phenomena in ferrites. Let us see
instead what ferrites can mean to those who get their callouses handling the soldering
iron.
First, one might ask, "Why ferrites?" Refreshing our memories from what the ham's
bible (29th edition, 1952, page 27) has to say about iron-core coils and their properties,
we can conclude that where currents run small - as in r.f. or i.f. transformer windings
for receivers - it would be very helpful to have high-permeability, low-loss cores.
For this purpose, component manufacturers have provided powdered-iron cores which
have permeabilities of the order of 125. Powdered-iron cores offer great improvement
at low and intermediate frequencies, but at the high frequencies losses still plague
us and the effective permeability of a powdered-iron slug is far below the true
permeability which may be obtained with a closed magnetic circuit (toroidal cores).
Now come the ferrites with maximum permeabilities ranging up to 4000 at 1 megacycle
and with a loss factor of 0.0003 at that frequency. With further increase in frequency,
the path divides at present into high-permeability materials with rapidly increasing
losses and lower-loss materials of much lower permeability. The field is an active
one and advances are being made daily, so it would be foolish to assume nothing
better is forthcoming - but just how soon would be hard to say:
Where the Losses Come From
High permeability and low losses in the r.f. range! How do we get it? Well, first
let us borrow a formula from the metallic-iron core designer. From it we can say
that the eddy-current losses (which are the principal losses to be considered) for
each lamination in the core are dependent upon a number of factors, some of which
we can monkey with and some of which we cannot:

where A = , a constant
V = volume of the lamination
Bmax = magnetic flux in the lamination
d = thickness of the lamination
ƒ = frequency
R = specific resistance of the lamination
Frequency and thickness both occur in the numerator as the square power and work
against you, and volume should be kept as low as possible. You can't help wanting
to use high-permeability material at high frequencies but what can you do about
the thickness? There is practical limitation to minimum thickness for a single lamination,
and to exceed that limit core manufacturers have turned to finely-powdered iron
particles. However, these cannot be packed together without insulating them from
each other, just as the laminations in a power transformer are coated with a film
of shellac. Plastics have been used to coat the powdered-iron particles, but the
amount of plastic necessary to coat completely the surface of each iron particle
becomes surprisingly large in these particle size ranges.
To get some idea of the surface area involved, start with a centimeter cube whose
surface area is 6 square centimeters. This amount of material, if reshaped, would
be approximately equal to one i.f. tuning slug. Cut it first into 8 equal cubes,
one-half centimeter on an edge, and the surface area has increased to 12 square
centimeters. Continuing to cut, we find that after 1000 cuts the surface area is
60 square centimeters and when the cubes are a millionth of a meter on an edge,
the total surface is 60,000 square centimeters or 64.5 square feet. The amount of
plastic insulation present in a powdered-iron core is therefore considerable, and
its principal effect is to "dilute" the iron and hence lower the overall true permeability
to about 125 from a value of 2500, typical for transformer iron. Worse yet, even
these small particles develop losses that can, at high frequencies, become serious
or prohibitive. Permeability decreases further because these fine-grained materials
have higher coercive force values, and as the area enclosed by the hysteresis loop
increases, so do the hysteresis losses. The use of open magnetic circuits (slugs)
instead of closed magnetic circuits (toroids) takes away a considerable chunk of
the true permeability, so that at 100 Mc. one can expect an effective working permeability
of about 5.
Referring back to the formula, the denominator is seen to contain the specific
resistance of the core material. For iron (no matter how small the particles may
be) this figure is about 0.00001. Dividing an already large numerator by such a
figure makes the answer come out extravagantly large, and there is no way to change
this materially so long as you are dealing with iron and its alloys; it's just the
nature of the beast.
Get acquainted with one of the newer magnetic materials that looks destined to
play an important part in the communications field. It is already responsible for
some of the high-Q coils that have gone into low-frequency "super-selective" i.f.
amplifiers.
Why Ferrites Are Better
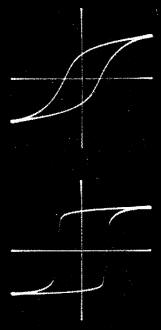
Oscillograms showing the types of hysteresis loops obtained with
ferrites. The flattened top and bottom of the lower trace show a type of characteristic
that lends itself well to on-off magnetic switching circuits.
Ferrites, however, are different. The various commercially available types have
specific resistance values ranging from 10,000 to 1,000,000,000 ohms per centimeter
cube. With this sort of figure in the denominator we no longer care about the thickness,
d. We can make the core of one solid piece to achieve maximum working permeability
and take full advantage of the magnetic properties, at least up to moderate frequencies.
Although V increases, this is more than offset by high specific resistance values
in the denominator.
At present, materials for use at 3 to 5 Mc. are available which have low loss
and high permeabilities (700-800). Toroidal coil forms of this material should provide
the highest efficiency yet achieved in transformers for this range and perhaps the
next 5 or 10 Mc. as well, for although losses increase rapidly with frequency, they
don't go out of sight yet. Many problems remain to be solved, but ferrites offer
more promise for r.f. cores than any material known.
At the very high frequencies, dielectric losses in ferrites become quite high
and we do not yet have the answer to very good cores for use above 10 to 20 Mc.;
but, even so, those now available are fully equal to or superior to powdered iron
at 100 Mc.
As we go from the very high to the ultrahigh range, oddly enough the dielectric
losses largely disappear in the range of 500 Mc. for some of the ferrites. Above
that, these materials are rather free of loss up to the range of 12,000 Mc., with
the exception of a range around 3000-4000 Mc. where large losses occur from magnetic
resonances within the crystal lattice structure of the materials.2 This
figure is variable and may be adjusted to lie outside a desired operating range.
What They Are
A few words about the composition and manufacture of ferrites may be of interest.
First of all, it has been found that a few simple inorganic chemical compounds,
known as ferrites, are magnetic (there are many other ferrites which are not magnetic).
The basic ideas are not new, as they are a logical extension and expansion based
on the magnetic lodestone whose origin is lost in Chinese antiquity. Hence, one
could easily say, "Why didn't I think of that?" Be that as it may, it was not until
about 1935 that any systematic studies were undertaken toward the results we now
have available. Commercially, the development is entirely a postwar one.
Magnetic ferrites are formed by chemical reaction of one or more oxides of certain
metals with a chemically equivalent amount of red oxide of iron. This reaction is
usually carried out between the mixed oxide powders at temperatures above 2000°
F. The various metal oxides which may be reacted with red oxide of iron are magnesium
oxide, black oxide of iron (which results in magnetite or the lodestone), nickel
oxide, copper oxide, cobalt oxide, manganese oxide and lithium oxide. These combinations
will each give a simple magnetic ferrite. However, complex mixtures of oxides are
usually employed, in order to give improved or special properties to the ferrite.
Oxides of zinc and cadmium form nonmagnetic ferrites, but are often blended with
the magnetic ones to reduce the temperature at which maximum permeability occurs
to a value near normal operating temperature.
Once the oxides have been reacted, the ferrite powder thus formed is used to
shape the piece or core desired. The usual practice is to mix a little binder with
the powdered ferrite and then press the desired piece in steel dies. The piece thus
formed will hang together until placed in a furnace for the final hardening or sintering
process. During the early stages of this heating, the binder is burned out of the
piece and later, at temperatures above 2000° F., the particles sinter or coalesce
into a dense, hard, somewhat brittle material, usually dark in color.
Applications and Possibilities
Ferrites have already seen many applications, and new ones are coming up practically
daily. Some of the better known applications see them used in recording heads, i.f.
transformer cores, magnetic modulators, horizontal sweep output transformer cores
for TV, yoke cores for TV, audio transformer cores (fine for the very high audio
frequencies), tuning slugs, "built-in" antennas, electronic computer "memory devices,"
pulse transformer cores, recording tape coatings, etc. One of the most intriguing
uses proposed is the microwave gyrator. In this application, a rod of ferrite is
inserted axially in a wave-guide where a polarized microwave may be rotated up to
90° upon passing through the ferrite in one direction but a reflected wave is
rotated 90° again in the same direction and hence it is possible to isolate
an oscillator or some other associated device from the rest of the microwave system.2
The limit to which ferrites may be applied is not now known, and it is not possible
even to speculate on it because of the continuous march of new ideas as the properties
of ferrites are further explored. For instance, it has been found that the shapes
of the hysteresis loops of ferrites can be monkeyed with (see photograph) on a practical
basis. The two hysteresis loops shown are for specimens prepared by the author,
and yet the chemical analysis of both specimens is the same. Fast-switching ferrites
suggest magnetic switches which will operate in 1 or 2 microseconds, and many other
interesting possibilities. Now it's up to you to try ferrites in your pet circuit
or scheme and see what comes of it. Who knows - you might make a million dollars!
Editor's Note: Ferrite parts are being produced by General Ceramics & Steatite
Corp., Keasbey, N. J.; Stackpole Carbon Co., St. Mary's, Pa.; Ferroxcube Corp. of
America, Saugerties, N. Y.; but all current production is of manufacturers' items
only, It is expected that Ferroxcube Corp., through its affiliate, the Sprague Products
Co., North Adams, Mass., will soon make ferrite parts available through regular
distributors.
1 Magnetic Circuits and Transformers, M.LT. Staff, p. 136, J. Wiley and
Sons, 1943.
2 Bell System Technical Journal, Vol. 31, pp. 1-31, 1952.
Posted October 11, 2023 (updated from original
post on 5/8/2015)
|