June 1955 Popular Electronics
Table of
Contents
Wax nostalgic about and learn from the history of early electronics. See articles
from
Popular Electronics,
published October 1954 - April 1985. All copyrights are hereby acknowledged.
|
This article from a 1955
issue of Popular Electronics discusses the state of the art of ultrasonic
transducers and equipment that uses them. Amazingly, of all the applications
that are mentioned, one is glaringly missing. Author Louis Garner, Jr., mentions
using ultrasonic transducers for measuring material thickness, detecting flaws
on and within materials and assemblies, cleaning by ultrasonic scrubbing,
soldering*, and motion detection for security systems. The missing items of
course is sonar
(sound navigation and ranging). The U.S. Navy was using sonar during World
War II, although it had been in development a couple decade earlier - similar to
radar's evolution. 15 - 20 kc (kHz) frequencies were typical in the day. Modern
ultrasonic cleaners use up to 40 kHz, and high resolution sonars run into the
low MHz. Oh, also missing is
ultrasound imaging like what is used for prenatal and other internal
imaging, but that was still in the experimental stage in the mid 1950s. BTW, I
worked with sonar systems as an electronics technician at the
Westinghouse
Oceanic Division in Annapolis, Maryland, in the 1980s.
* See the interesting information on
ultrasonic soldering on the S−Bond Technologies website.
Silent Sound
By Louis E. Garner, Jr.
Powerful sound waves radiated by mechanical transducers find a multitude of valuable
applications in industry.
Ultrasonic Instruments, industry's newest tools, are used for such varied tasks
as measuring the wall thickness of metal tanks, checking forging ingots for flaws,
locating defects in railroad tracks, soldering aluminum and other hard-to-solder
metals without fluxes, protecting plants and offices against intruders, and for
machining metals and other hard materials. Ultrasonic cleaning machines are used
for everything from tiny laboratory instruments to aircraft parts, from gears to
delicate optical lenses.
Ultrasonic refers to those sound frequencies above approximately fifteen thousand
cps. The upper limit is very high - into the megacycles (millions of cycles per
second). Since ultrasonic signals are not audible, they are frequently called "silent
sound."
A transducer is a device for changing energy from one form to another. Earphones
and loudspeakers are transducers, for they serve to change electrical energy into
acoustic energy. Transducers are the important links between the electronic circuits
which produce, amplify, and measure ultrasonic signals and the materials which are
being processed or tested by the ultrasonic instruments.
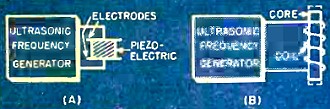
Fig. 1 - Two basic transducer designs are shown above. Drawing
(A) has a crystal element and drawing (B) a magnetostrictive core. Actual element
movement in both cases is extremely small.
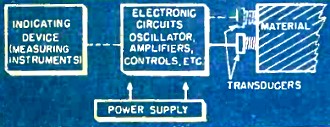
Fig. 2 - A simplified block diagram of industrial ultrasonic
equipment.
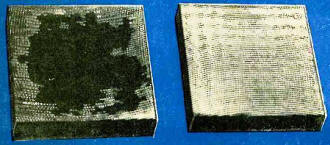
Fig. 3 - These plates illustrate the efficiency of ultrasonic
cleaning. Both were soiled with a black grease pencil. The clean plate was cleaned
in two seconds using a solvent activated by ultrasonics.
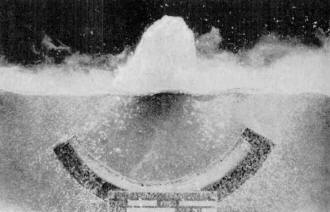
This photo shows the violent agitation of a liquid excited by
the curved ultrasonic transducer immersed in the solution.
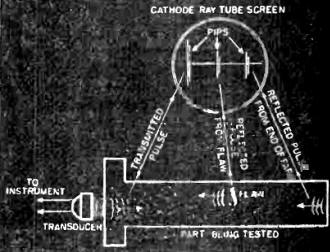
Fig. 4 - Pulses of ultrasonic energy are reflected by flaws and
displayed on a cathode ray tube.
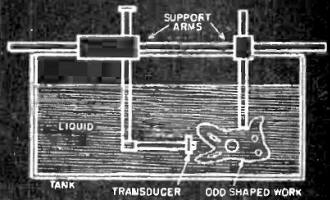
Fig. 5 - Illustration of a method for examining odd-shaped metallic
pieces for flaws using ultrasonic waves.
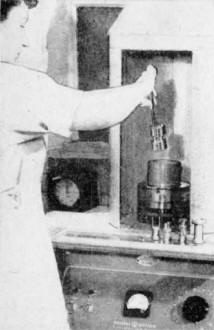
A General Electric ultrasonic generator is shown being used at
the Holley Carburetor Co, to clean a jet engine fuel control part.
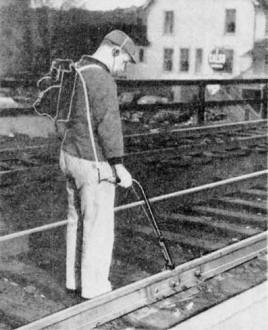
Using a portable ultrasonic flaw detector to check a railroad
track rail for defects or cracks.
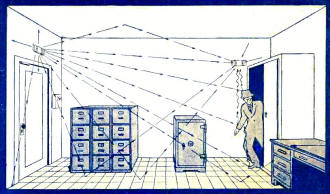
Fig. 6 - This sketch illustrates the operation of the ultrasonic
alarm system.
Industrial ultrasonic transducers are generally made up either of piezoelectric
materials or magnetostrictive elements. A piezoelectric material is a substance
whose physical dimensions change when a voltage is applied to it, producing a mechanical
force. The converse is also true in most cases - when mechanical force is applied
to the material, an electrical voltage may be generated. The mechanical force may
be pressure or a twisting or bending action. Typical piezoelectric materials are
quartz crystals, Rochelle salts, barium titanate, and certain other ceramics. Crystal
and ceramic microphones and phonograph cartridges are everyday examples of piezoelectric
transducers.
A magnetostrictive element is a core of magnetic material surrounded by an energizing
coil. When a piece of material is magnetized, the individual molecules of the substance
"line up" in order. This results in a minute change in the material's length. When
ultrasonic electrical energy is supplied to the coil, the core is first magnetized
in one direction, demagnetized, then magnetized in the opposite direction. Since
the core length changes with each magnetization, the result is a change from electrical
energy (in the energizing coil) to mechanical movement (lengthening and shortening
core). Nickel and its alloys are frequently used as cores for magnetostrictive elements.
A simplified block diagram for industrial ultrasonic equipment is given in Fig.
2. With modifications, this diagram applies to almost all of the ultrasonic instruments
in current use. The "heart and brains" of the equipment are the electronic circuits
which generate and control the high frequency electrical signals. In the case of
measuring instruments, there may be circuits producing, detecting, and amplifying
ultrasonic signals. There will be one or more transducers to convert the high frequency
electrical energy into ultrasonic vibrations in the material being tested or processed.
Where measurements are involved, there will be an indicating device.
Cleaning Parts: One example of the capabilities of ultrasonic
instruments is given by the sample plates in Fig. 3. Both of these deeply serrated
metal plates were soiled with a black grease pencil. The clean one was given a 2-second
rinse in a solvent activated by ultrasonic vibration; the other was given a rinse
two and half times as long in the same solvent, but without activation. It required
10 minutes for complete cleaning without ultrasonics - 300 times as long as with
activation. In some cases, the transducer may be shaped to focus or to concentrate
the ultrasonic vibrations. The frequencies used for ultrasonic cleaning range from
as low as 15 kc. to 1 mc. and higher.
The efficiency of an ultrasonic cleaner results from two actions : the vibratory
motion given to the liquid cleaner by the ultrasonic energy; and the action called
cavitation, a "cold-boil" which results when the vibrating liquid is torn into small
vacuum pockets. As these pockets form and collapse, they create strong localized
pressures, bombarding the parts being cleaned from every direction, and blasting
off dirt and other foreign matter.
Thickness Measurement: To measure the thickness of the metal
in a large tank, or in a ship's hull, where only one side can be reached, is not
impossible with an ultrasonic thickness gauge.
Several methods may be used but portable instruments frequently employ the principle
of resonance. A transducer, driven by an electronic oscillator, is placed in contact
with one side of the material to be tested. The ultrasonic wave travels through
the material in a narrow beam and is reflected by the opposite surface. At certain
frequencies the transmitted wave and the reflected wave will reinforce each other,
resulting in an increase in the intensity of the wave in the material. The frequencies
at which the reinforcement occurs depend on the thickness of the material and the
velocity of sound through it. Since the velocity of sound is constant for a particular
material, the determination of the fundamental frequency of resonance (where reinforcement
occurs) is a reliable measure of the thickness of the material.
Inspection and Test: The "echo" principle is used in industrial
test instruments wit h ultrasonic vibrations taking the place of radio or audible
sound waves. The reflectoscope may be used for checking large metal billets for
defects, locating flaws in castings and forgings, checking parts for interior defects,
evaluating welds, and checking the physical dimensions of metal parts where only
one end or side may be reached.
In operation, a transducer is placed against one end of the piece to be tested
and "beams" pulses of ultrasonic energy through the material (see Fig. 4). These
pulses travel to the end of the piece and are reflected back to the transducer,
where they are detected. If there are cracks or holes in the piece, these flaws
also cause reflections. The transmitted signal and all of the reflected pulses are
displayed as "pips " on the screen of a cathode-ray tube. The relative distance
between t he first pip and succeeding pips on the tube's screen is proportional
to the distance between the point where the transducer is placed and the distance
to the flaws or to the end of the piece. Thus, the instrument shows both defects
and their approximate location. If the piece has an irregular shape, it may be immersed
in liquid for testing, as shown in Fig. 5. The liquid transmits the ultrasonic vibrations
from the transducer to the piece.
Ultrasonic Soldering: Soldering aluminum is difficult because
oxide films form so rapidly. Success depends on clean metal surfaces and strong
flux. After the soldering is completed, every trace of flux must be removed to prevent
corrosion. Ultrasonic soldering instruments, however, have simplified this job.
A magnetostrictive transducer, operating at about 20 kc., vibrates the metal and
literally rips up oxide films, allowing the solder to form a strong union with the
heated metal.
Plant Protection: Most modern industrial plants are fairly well protected, either
by full time guard staffs or by various electronic burglar alarms, including "electric
eye" systems, electronic fences, closed circuit television observation stations,
and similar protective devices. But only ultrasonics can guard against the intruder
who hides inside during working hours and works by night.
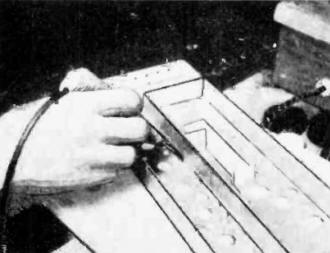
A small hand tool is used to make a soldered fillet in a grounded
aluminum chassis.
The operation of an ultrasonic alarm system is illustrated in Fig. 6. High frequency
sound waves are "broadcast" by the transmitting transducer, just above the door.
These ultrasonic signals bounce off the floor, ceiling, walls and furniture, literally
filling the room with silent sound. The signals are picked up by the receiving transducer.
As long as the transmitted and received signals are the same frequency, the room
is secure and protected. But if anything should move within the room, the frequency
of the signal picked up by the receiving transducer changes slightly. Electronic
circuits are constantly comparing the frequencies of the transmitted and received
signals, and when the small frequency change occurs, an alarm is sounded.
Truly, the surface has barely been scratched as far as potential applications
of ultrasonic equipment are concerned. We may expect to see it used in every branch
of industry, in the home, in business, and in medicine. Ultrasonic drills have been
used in dentistry (see "Dentistry - the Painless Way," Popular Electronics, November,
1954.) Ultrasonic vibrations have been used to accelerate the pollination of plants.
Laundry work has been done with ultrasonics. In the future, "smog" may become a
thing of the past as ultrasonics is used to coagulate and precipitate stoke and
dust.
Future applications will be covered in other issues of Popular Electronics.
Posted July 19, 2019
|